МОДЕЛИРОВАНИЕ ПРОЦЕССОВ ГОРЕНИЯ И ТЕПЛООБМЕНА В ДВС С ИСКРОВЫМ ЗАЖИГАНИЕМ С УЧЕТОМ ФОРМЫ КАМЕРЫ СГОРАНИЯ
М. А. Ильина, М. Ю. Свердлов, Д.Д. Матиевский, П. К. Сеначин
ВВЕДЕНИЕ
Описание процесса горения в ДВС является весьма сложной задачей в связи с многообразием явлений, происходящих от момента воспламенения топливно-воздушной смеси до момента открытия выпускного клапана. Несмотря на последние достижения, необходимость в изучении внутрикамерных процессов продолжает оставаться весьма актуальной. Процесс сгорания топлива является основным процессом, в котором теплота топлива превращается в механическую работу [1-4]. Он стал предметом исследований, которые ведутся во многих направлениях, и их актуальность непрерывно возрастает. При этом принципиальным является тот факт, что основа исследований и количественных обобщений лежит на пути создания физической модели рассматриваемых явлений и описания их с помощью системы дифференциальных уравнений [5-7].
Использование численных методов моделирования, ориентированных на применение ЭВМ, значительно расширяет возможности математического моделирования, позволяя включить в модель факторы, не учитываемые ранее. Детальный анализ динамики горения топлив предполагает строгий учет всех физических процессов, в том числе процессов конвективного теплообмена между свежим газом и продуктами горения и конструктивными элементами оболочки [8].
МАТЕМАТИЧЕСКАЯ МОДЕЛЬ
В основе математической модели горения газовой смеси в двигателе с искровым зажиганием лежит предположение, что рабочее вещество в цилиндре в процессе сгорания разделено фронтом пламени на две зоны, которые будем называть зоной заряда (зоной свежих продуктов) и зоной продуктов сгорания. Поскольку конвективный и радиационный теплообмен имеют различную физическую природу и определяющие показатели, имеет смысл проводить анализ существующих зависимостей для оценки конвективной и радиационной составляющей суммарного теплового потока раздельно. В данной работе учитывается процесс конвективного теплообмена свежего газа и продуктов горения с элементами оболочки, включающей поверхности камеры сгорания, цилиндра и поршня, имеющие различную температуру. С целью практического применения данной модели в программу заложена возможность варьирования рабочих параметров ДВС и его характеристик, основными из которых являются геометрия камеры сгорания и параметры смеси в момент зажигания.
Форма и поверхность пламени при сгорании гомогенных горючих смесей в двигателях зависит от геометрии камеры сгорания и существенно влияет на основные черты динамики процесса: скорость превращения вещества, скорость нарастания давления, распределение скоростей газа и т.д. Рассматриваются особенности динамики сгорания смеси и экономические (термодинамические) характеристики цикла для ДВС с искровым зажиганием, имеющих камеры сгорания различной геометрии. При построении математической модели рабочего процесса сгорания гомогенной смеси рассмотрены случаи, учитывающие процесс распространения волны горения (турбулизированного нормального пламени) в сферических сечениях камеры сгорания цилиндрической формы с точкой зажигания на оси (Модель 1, рис.1А), со смещенной точкой зажигания (Модель 1А, рис.1В) и асимметричной (клиновидной) камеры с точкой зажигания в вершине клина (Модель 7, рис.1С). Полагаем, что эти модели являются предельными (или близкими к ним) как в отношении геометрии камеры сгорания, так и расположения точки зажигания. Предполагается, что, несмотря на турбулентный характер горения, распространяющееся пламя тонкое, то есть размер камеры велик по сравнению с шириной зоны пламени. Рассматривается медленное фронтальное горение газа в закрытой теплоизолированной системе, поэтому давление одинаково во всех точках камеры сгорания и изменяется только во времени. Как обычно, основными независимыми геометрическими параметрами двигателя полагаем радиус кривошипа r, диаметр поршня D и геометрическую степень сжатия ε. В качестве независимой переменной, аналогичной времени, принят угол поворота коленчатого вала j
. Параметры смеси в момент зажигания, соответствующий углу поворота коленчатого вала j
i, предполагаются известными.
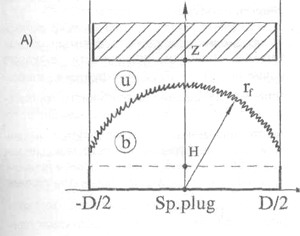
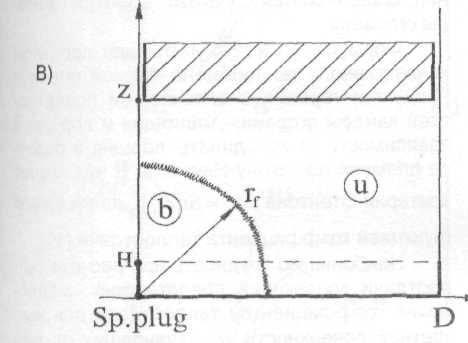
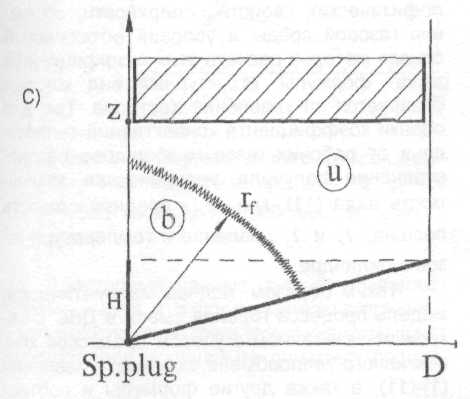
Рис.1 Распространение фронта пламени в камере сгорания двигателя с искровым зажиганием:
rf- радиус сферического фронта пламени; z- координата поршня; D- диаметр поршня; H- высота камеры сгорания; Sp.plug-точка, в которой происходит зажигание смеси.
Рабочий объем системы определяется известной в динамике двигателей приближенной формулой для аксиального механизма [9]:

При наличии двух зон необходимо записать два термических и два калорических уравнения состояния (одно из которых является уравнением динамики давления), а также учесть процессы теплообмена этих зон с элементами ограничивающих поверхностей. Система уравнений, описывающих процесс горения смеси, включает следующие уравнения:
динамики давления
(1)


В систему уравнений входят:
:
p
= p/pi – давление, q
u = Tu/Ti – температура, w = V/Vi - объем, x = m0/mi – массовая доля продуктов горения, ST = Su/S
- нормальная скорость пламени;
-параметры процесса:
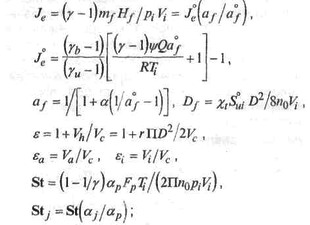
-постоянные:
R- универсальная газовая постоянная; Cp,Cv- мольные теплоемкости; Q,Hf- тепловой эффект химической реакции (на моль горючего компонента) и удельная энтальпия сгорания топлива; mf,a
,af- - масса топлива, поступающего в камеру сгорания за один цикл, и его мольная стехиометрическая и действительная доли; а - коэффициент избытка воздуха; s- порядок химической реакции; Si – “нормальная” скорость турбулентного пламени; Su- текущая нормальная скорость пламени;
- фактор турбулизации пламени [10-12]; ui – скорость турбулентного переноса; S
- нормальная скорость пламени для смеси стехиометрического состава в момент зажигания; n - частота вращения коленчатого вала; l
= r/l- отношение радиуса кривошипа к длине шатуна; D,Vc,Vh- диаметр поршня, объемы камеры сгорания и цилиндра.
Индексы i,u,b относятся к моменту зажигания смеси, свежей смеси и продуктам горения соответственно. Необходимый для расчета процесса динамический параметр J
вычисляется по уточненной формуле при
c учетом того, что не все выделившееся тепло идет на повышение внутренней энергии и совершение работы.
Система (1)-(11) дополнительно включает уравнения для расчета функции относительной площади поверхности активного пламени f(p
)=Ff/Fp и функции относительных площадей конвективного теплообмена fj = Fj/Fp . Эти функции зависят от текущих переменных и определяются численным решением уравнений, связывающих между собой значения радиуса фронта пламени rf и поршня z и объема продуктов горения Vb [13]. Площади поверхностей, контактирующих со свежим газом и продуктами горения, определяются с учетом геометрии камеры сгорания.
Формулы (9) и (10) учитывают процессы конвективного теплообмена свежей смеси и продуктов горения с элементами поверхностей камеры сгорания, цилиндра и поршня в зависимости от координаты поршня и радиуса пламени по закону Ньютона. В них входит критерий Стентона Stj =St(aj), являющийся функцией коэффициента теплоотдачи (11).
Наибольшую трудность при расчете теплоотдачи конвекцией представляет определение коэффициентов теплоотдачи для конкретной поверхности aj, зависящих от теплофизических свойств поверхности, состояния газовой среды и условий обтекания. В основе методов расчета этих коэффициентов лежат формулы, структурный вид которых базируется на уравнении Кострова. Так, для оценки коэффициента конвективной теплоотдачи от рабочих газов наибольшее распространение получила эмпирическая зависимость вида (11), где ст- средняя скорость поршня, P2, и Т2 давление и температура газов в цилиндре.
Таким образом, полная математическая модель процесса горения смеси в ДВС с искровым зажиганием с учетом процессов конвективного теплообмена включает уравнения (1)-(11), а также другие формулы и соотношения. Система уравнений решалась численно методом Рунге-Кутта 4-го порядка при различных углах зажигания j
i, степени сжатия ε и частоты вращения коленчатого вала n . Интегрирование производилось по малым интервалам времени, соответствующим 0,02° угла п.к.в.
Заметим, что значения температур поверхностей деталей лежат в сравнительно узком интервале, что позволяет считать их постоянными в процессе тепловыделения и равными соответственно Тl = Тс, T2 = Td , T3 = Тр. Температуры продуктов горения и свежей смеси вычисляются на каждом шаге интегрирования системы уравнений, описывающих процесс горения и теплообмена конвекцией.
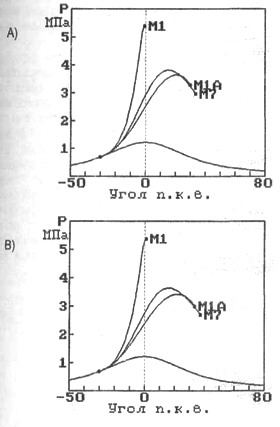
Рис. 2. Динамика сгорании смеси в камерах с различной геометрией при
ε = 7,0; j
i·=-30 град. п.к.в.: А) п =2000 мин-1, В) η =4000 мин-1.
Полученные данные (рис. 2) позволяют сделать вывод, что форма камеры сгорания и место расположения точки зажигания оказывают существенное влияние на динамику процесса.
Для исследования зависимости влияния рабочего процесса от формы камеры сгорания индикаторные диаграммы, полученные численным моделированием, сравнивались по двум параметрам: продолжительности сгорания и максимальному давлению в цилиндре. Наименьшее время полного сгорания имеет симметричная камера с точкой зажигания на оси (Модели 1). Для двигателя с цилиндрической камерой сгорания со смещенной точкой зажигания (Модель 1А) процесс сгорания смеси сильно затянут (примерно в два раза), еще больше он затянут для клиновидной камеры с асимметричным зажиганием (Модель 7). Видно, что в Модели 7 и Модели 1А максимальное (и среднее) индикаторное давление значительно ниже, чем в Модели 1.
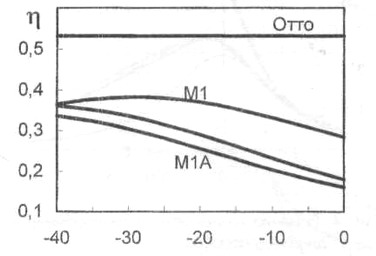
Рис. 3. Зависимость индикаторного КПД цикла от угла зажигания
φί для камер с различной реальной геометрией при степени сжатия ε =10,0 и частоте n =2000 мин-1 в сравнении с циклом Отто.
При исследовании влияния формы камеры сгорания ставилась задача оценить ее влияние на КПД процесса в сравнении с циклом Отто, для которого КПД определяется уравнением:
.
Из полученных результатов, представленных на рис.3, видно, что КПД реальных циклов сгорания смеси значительно ниже, чем идеализированного цикла Отто. Также дано численное подтверждение факта заметного влияния на динамику сгорания смеси и индикаторный КПД цикла формы камеры сгорания и места расположения точки зажигания. Для Модели 1 КПД имеет максимум при угле зажигания φί »
-30 град п.к.в., а для Моделей 1А и 7 этот максимум расположен дальше от ВМТ и имеет значительно больший градиент на графике. Форма камеры сгорания (или близкая к ней) в Модели 1 и симметричное расположение точки зажигания, по-видимому, оптимальны для конструкторских решений.
В работе дано подтверждение того факта, что конвективный теплообмен оказывает существенное влияние на динамику процесса сгорания. На индикаторных диаграммах (рис.4), описывающих динамику процесса, наблюдается падение максимального давления в цилиндре и увеличение длительности горения. Причем процесс горения затягивается все больше по мере приближения момента зажигания к ВМТ.
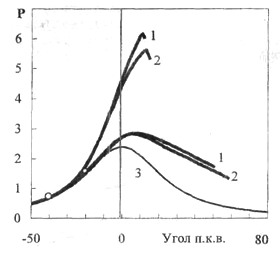
Рис. 4. Влияние конвективного теплообмена на динамику процесса:1- без теплообмена; 2- с учетом теплообмена; 3- сжатие-расширение инертной смеси
.
Конвективный теплообмен в цилиндре ДВС всецело определяется характером движения рабочего тела, который существенно зависит от конструктивных особенностей двигателя. В связи с этим особое внимание в работе уделяется исследованию процесса передачи тепла конвекцией в стенки камеры сгорания с различной геометрией.
Представляется интересным рассмотреть зависимость конвективного теплообмена от формы камеры сгорания в следующих аспектах:
- а)оценки влияния формы камеры сгорания на характер теплообмена и количество отведенной теплоты;
- б)оценки теплообмена через поверхности головки, поршня, гильзы;
- в)степени влияния теплообмена на отдельных участках рабочего цикла.
Целесообразность исследований в отмеченных направлениях предопределяется их практической значимостью, выражаемой в получении ответа на вопрос: на каком участке рабочего цикла, через поверхность какой детали и какую форму теплообмена следует ослаблять с целью достижения максимального эффекта в снижении коэффициента неиспользования теплоты вследствие ее отвода от рабочего тела при положениях поршня между мертвыми точками и увеличении индикаторного КПД двигателя.
Анализ результатов численных исследований показал, что уменьшение тепловых потерь при конвективном теплообмене на 3-4% приводит к увеличению КПД в среднем на 1,5%. Потеря теплоты конвекцией приводит к снижению КПД двигателя с искровым зажиганием. Для анализа влияния тепловых потерь на индикаторный КПД проводились численные эксперименты с учетом теплообмена и без него. В результате многочисленных числовых экспериментов выяснена следующая закономерность: изменение частоты вращения коленчатого вала и степени сжатия не оказывает существенного влияния на характер изменения потерь и КПД при изменении угла зажигания, а приводит лишь к незначительному изменению потерь по величине.
На рис. 5. приведены результаты численных экспериментов, позволяющих проанализировать влияние формы камеры сгорания на суммарные потери тепла при конвективном теплообмене. Численные эксперименты проводились для различных значениях степени сжатия (ε = 7,0; 8,5 и 10,0) и числа оборотов коленчатого вала (n=2000; 4000 и 6000 мин-1). При всех значениях варьируемых параметров наибольшие потери составляют для симметричной камеры сгорания с точкой зажигания на оси (Модель 1). Смещение точки зажигания приводит к сокращению потерь примерно в два раза, при этом величина потерь оказывается меньше, чем для клиновидной формы камеры сгорания.
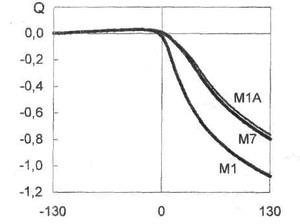
Рис.5. Влияния формы камеры сгорания на характер теплообмена и количество отведенной теплоты
Анализ результатов численного моделирования показывает, что форма камеры и положение точки зажигания играют важную роль в формировании теплообмена. Наименее выгодной с точки зрения количества потерянной теплоты является симметричная камера сгорания с точкой зажигания на оси. Вместе с тем эта форма камеры является оптимальной по КПД. Это обстоятельство объясняется ростом коэффициента неиспользования теплоты от несвоевременности ввода теплоты из-за увеличения длительности горения во времени в моделях 1А и 7 по сравнению с коэффициентом потерь теплоты вследствие ее отвода от рабочего тела.
В настоящее время вопросы распределения теплообмена между деталями, ограничивающими объем камеры сгорания, являются наименее разработанными. Достоверность определения этих данных играет решающую роль в оценке температурного и напряженно-деформированного состояния деталей центральной поршневой группы и в разработке практических рекомендаций по конструктивному исполнению теплонапряженных узлов и деталей камеры сгорания. Практическую значимость распределение тепловых потерь по поверхностям приобретает при решении задачи достижения максимального эффекта в снижении коэффициента неиспользования теплоты вследствие ее отвода от рабочего тела и увеличении индикаторного КПД. Сложность и недостаточная изученность этих процессов не позволяли ранее построить единую теорию процессов переноса энергии. При расчете процесса сгорания по предлагаемой модели с помощью ЭВМ появляется возможность воспроизвести картину распределения тепловых потоков через поверхности головки камеры сгорания, поршня и гильзы цилиндра при различной конфигурации камеры сгорания и оценить степень влияния конвективного теплообмена на отдельных участках рабочего цикла.
Из графиков, приведенных на рис. 6., следует, что варьирование числа оборотов коленчатого вала, степени сжатия и изменение формы камеры сгорания не оказывает существенного влияния на характер распределения тепловых потерь через поверхности головки, поршня и гильзы цилиндра. Так, численный эксперимент показывает, что наибольшие потери тепла происходят через поверхность камеры сгорания. Это объясняется тем, что поверхность камеры более длительное время контактирует с продуктами горения, имеющими более высокую температуру. Как показывают исследования, основные потоки, формирующие тепловую нагрузку поршня, цилиндра и камеры сгорания, образуются на тактах горения и расширения. Построенная модель отражает и тот факт, что при движении внутри цилиндра заряд, соприкасаясь со стенками, имеющими более высокую температуру, подогревается. Степень его подогрева зависит от продолжительности впуска, скорости движения, а также от разности температуры стенок и свежего заряда. На такте сжатия тепловой поток вследствие конвективного теплообмена направлен от стенок к рабочему телу. Это приводит к незначительному подъему кривой на участке от закрытия выпускного клапана до начала горения.
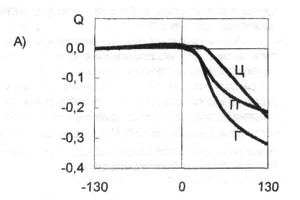
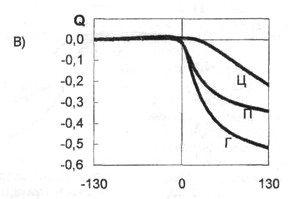
Рис. 6. Распределение тепловых потерь по по поверхностям для Модели
1 при n = 2000 мин-1, ε = 7,0 и различных углов зажигания: а) j
i = -10° п.к.в; б) j
i = -30° п.к.в.
Влияние формы камеры сгорания на распределение тепловых потоков через поверхности головки, поршня и цилиндра при различной конфигурации камеры сгорания и степень влияния конвективного теплообмена на отдельных участках рабочего цикла можно оценить по рис. 7. Видно, что при изменении количества отведенной теплоты через каждую из ограничивающих поверхностей за цикл характер распределения тепловых потерь при конвективном теплообмене не меняется.
Построенная модель является универсальной методикой оценки качественных и количественных характеристик теплообмена, причем раздельно по конвективной и радиационной составляющим, учитывая их различную природу и сущность. Результаты численных исследований и их сопоставление с экспериментальными данными позволит проанализировать влияние теплообмена на динамику процесса, термодинамические (индикаторный КПД цикла и др.) и экономические показатели цикла и разработать мероприятия по улучшению характеристик двигателя.
Остановимся на еще одном важном результате численного моделирования. Одним из главнейших факторов, определяющих динамику процесса сгорания, является кинетика процесса сгорания или скорость сгорания. Кинетический закон сгорания характеризуется уравнением выгорания топлива в двигателях x=F(f), характеризующим изменение доли сгоревшего заряда x во времени (то есть функцию тепловыделения).
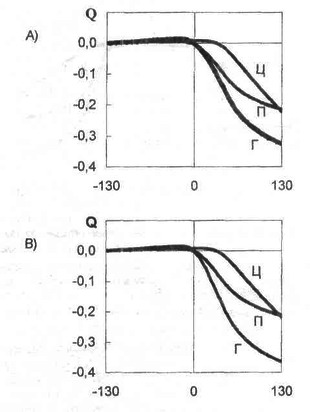
Рис. 7. Распределение тепловых потерь по поверхностям головки, поршня и цилиндра
при угле зажигания j
i- = -30° п.к.в.: А) Модель 1А; В) Модель 7.
Наибольшее распространение получило полуэмпирическое кинетическое уравнение выгорания И.И. Вибе, включающее параметр т, однозначно определяющий характер протекания процесса сгорания по времени

где j
i - угол зажигания, j
z - условная продолжительность сгорания, т - показатель характера сгорания топлива. Согласно И.И. Вибе [1], показатель характера сгорания имеет оптимальное значение т »
1,5, которое соответствует относительному времени максимума скорости сгорания t/tz »
0,38. Однако, как утверждает автор, оптимальное значение т еще не достигнуто ни в карбюраторных двигателях, ни в дизелях. Для серийных ДВС с искровым зажиганием этот показатель обычно лежит в пределах от 3 до 4. Такие его значения принимаются также при тепловом расчете нормативным методом.
В предлагаемой математической модели уравнение массовой скорости горения (7) получено не на эмпирических данных, а опираясь на теорию горения. Численное моделирование дает возможность получить информацию о влиянии геометрии камеры сгорания на кривую тепловыделения, экспериментально получить которую весьма сложно.
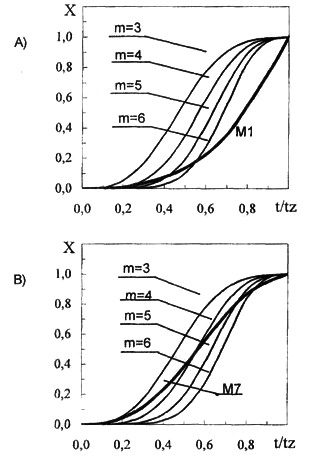
Рис. 8. Функция тепловыделения И. И. Вибе при различных значениях показателя
m в сравнении с реальными законами сгорания: А- симметричная камера (Модель 1), В-клиновидная камера (Модель 7)
На рис. 8 приведены кривые тепловыделения для камер сгорания различной геометрии в сравнении с вычисленной по формуле И.И. Вибе при различных значениях показателя сгорания т. Из рисунка видно что для клиновидной камеры сгорания с удаленной точкой зажигания (Модель 7) функция И.И. Вибе имеет лучшую корреляцию с реальным законом сгорания, чем для симметричной цилиндрической камеры сгорания (Модель 1). Однако расчеты показывают, что даже для отдельных случаев приближение нельзя считать достаточным. Полагаем, что этот вопрос требует специального анализа.
ВЫВОДЫ
1. Построена математическая модель рабочего процесса в ДВС с искровым зажиганием, учитывающая процессы горения смеси во времени и пространстве при различных формах камеры сгорания и расположении точки зажигания.
2. В математическую модель включены уравнения, учитывающие процессы конвективного теплообмена поверхностей, ограничивающих рабочий объем и имеющих различную температуру, с зонами свежей смеси и продуктов горения в процессе сгорания смеси.
3. Проведены численные исследования влияния формы камеры сгорания на динамику сгорания смеси и индикаторный КПД цикла при различных углах зажигания, степенях сжатия и частоты вращения.
4. Исследовано влияние конвективного теплообмена на динамику процесса и влияние формы камеры сгорания на характер теплообмена и количество отведенной теплоты, включая распределения тепловых потерь по поверхностям теплообмена.
ЛИТЕРАТУРА
- Вибе И.И. Теория двигателей внутреннего сгорания: Конспект лекций. Челябинск: Изд-во Челябин. политехи, ин-та, 1974.252 с.
- Петриченко P.M. Физические основы внутрицилиндровых процессов в двигателях внутреннего сгорания: Учебное пособие. Л.: Изд-во Ленингр. ун-та, 1983.244 с.
- Клепов Ю.В. Самовоспламенение метаноловоздушной смеси перед фронтом пламени в камере сгорания ДВС // Кинетика и горение. Матер.
VIII Всесоюз. симпоз. по горению и взрыву. Черноголовка: Изд-во ОИХФ АН СССР, 1986. С. 54-57.
Двигатели внутреннего сгорания: Устройство и работа поршневых и комбинированных двигателей.; Под. ред. Орлина А.С. Круглова М.Г. М.: Машиностроение, 1980.288 с.
Куценко А.С. Моделирование рабочих процессов двигателей внутреннего сгорания на ЭВМ. Киев: Наук. думка, 1988.104 с.
Ramaswamy M.C., Cupta M.C. Some Aspects of Flame Quenching in a Spark Ignition Engine // Archiwum Termodinamiki i Spalania. 1979. V. 18, №3. P. 405-418.
Moses E., Yarin A.L. and Bar-Yoseph P. On Knocking Prediction in Spark Ignition Engines // Combust. Flame. 1995. V. 101, N.. P. 239-261.
Ильина М.А., Сеначин П.К., Свердлов М.Ю. Моделирование конвективного и радиационного теплообмена в ДВС с искровым зажиганием. Проблемы гидродинамики и тепломассообмена: Сборник научн. статей / Под ред. А.М. Сагапакова. Барнаул: Изд-во Алт. ун-та, 1999. С. 73-80.
Генкин К.И. Рабочий процесс и сгорание в двигателях с искровым зажиганием // Сгорание в транспортных поршневых двигателях. М.: Изд-во АН СССР, 1951. С. 102-133.
Beretta G.P., Rashidi M. and Keck J.C. Turbulent Flame Propagation and Combustion in Spark Ignition Engines // Combust. Flame. 1983. V. 52. P. 217-245.
Чудаков Е.А. Основные проблемы сгорания топлива в автотракторных двигателях // Сгорание в транспортных поршневых двигателях. М.: Изд-во АН СССР, 1951. С. 102-133.
Карпов В.П. Горение газообразных смесей в двигателях. М.:Машгиз, 1951.120 с.
Ильина М.А., Матиевский Д.Д., Сеначин П.К., Свердлов М.Ю. Новый подход к проблеме моделирования сгорания смеси в ДВС с искровым зажиганием. Ползуновский альманах. 1999. №2. С. 101-110.